改善活動とは?
当社のよいところは、常に挑戦し続ける取り組みができることです。
当社では改革、革新、改新、改善等の取り組みが行われていますが、その中の一つである改善は、常に目標を持ち物事をよい方向に導くための活動です。具体的には現場力を向上するために「改善メモ」という仕掛けを利用しています。更に、改善の取り組みは、物事の創造力を高めるための初歩的な手段としても用いています。
当社では改革、革新、改新、改善等の取り組みが行われていますが、その中の一つである改善は、常に目標を持ち物事をよい方向に導くための活動です。具体的には現場力を向上するために「改善メモ」という仕掛けを利用しています。更に、改善の取り組みは、物事の創造力を高めるための初歩的な手段としても用いています。
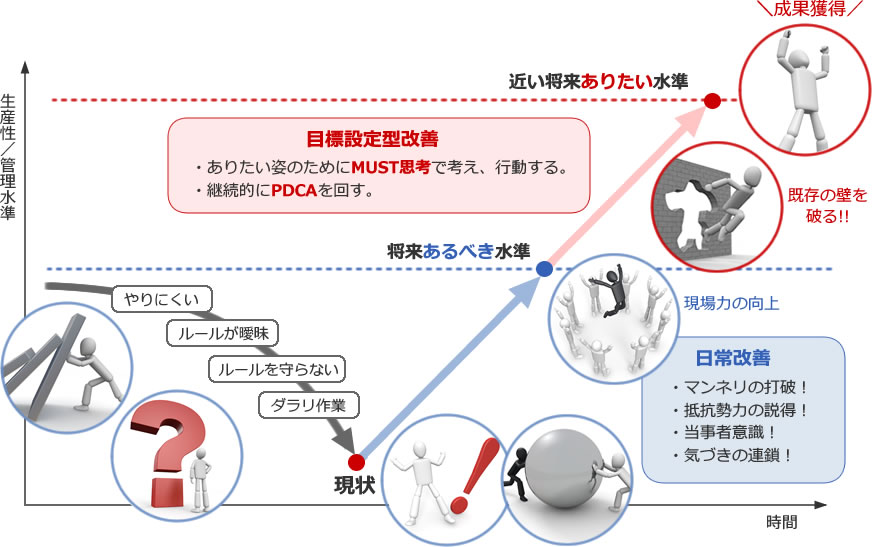
過去の改善事例
キャビネットのラベリング
-
-
改善前(問題点)中の見えないキャビネットの引き出しに直接テプラでラベリングしたり、その上から両面テープで張り直していたり、見栄えが悪いものになっていた。
改善後(対策)引き出しの見出しになる専用の様式を作成し、出力した後にラミネート加工をした。その裏にマグネットシートを貼り、キャビネットの引き出しにくっつけた。見栄えも良く、貼り直しもスムーズになった。
効果各書類を収納する時間 約30分/月
各書類を探す回数 約2回(約10分)/月
見出しがそろっていることで、探しやすくなるのでこれらの作業時間が半減する。
【生産性】 4時間UP
【コスト】 2300円×4時間=9200円 9200円コストdown
2022年1月
その他の改善実例
乾電池管理ルールの浸透
-
改善前(問題点)電池を充電する際の管理方法がローカルルールとなっていた。新入社員も増え、全員に浸透していなかった。
改善後(対策)表示の一手間で解決!
浸透していないローカルルールを対策していくことも改善の一手です。
2023年10月 -
オリジナル器材のオーダー管理
-
改善前(問題点)長年使用してきた測定器材を新調しようとしたが、過去メーカーへオーダーメードしたこと以外記録が残っておらず新調するのに手間取った。改善後(対策)各部の寸法とパーツの大きさや購入先を記した図面を作成した。
今後も同器材を使用していくため寸法を取ったり部品を探す手間を解消した。効果・寸法をとる時間、部品を探す時間down
・オリジナル器材の伝承
2023年8月 -
機器取扱いマニュアル作成
-
改善前(問題点)検出器の感度低下に伴い、メーカーからガラス窓部の掃除を推奨されたが、説明書の解体方法の記載が不透明であった。改善後(対策)各手順を写真で撮影して並べた簡易的な分解手順書を作成した。
工程ごとに注意点も記載し破損防止にもつながる。効果・整備性向上
・破損防止
2022年8月 -
給水タイマーの設置
-
改善前(問題点)精製水の給水時、水が自動で停止しないので満水になるまで目が離せず、作業を停止していた。改善後(対策)満水になるまでの時間を計測し、専用のキッチンタイマーをセットした。タイマーが鳴ることで満水が分かるためタンクから離れて別作業をすることが可能になった。効果【生産性】
一回当たり65秒
1日3回×6人=19.5分
1カ月で6.5時間生産性UP
【コスト】
約6.5時間×2,300円=14,950円down
2022年5月 -
ろ紙ホルダーキャップ封緘時の改善案
-
改善前(問題点)TDI測定用のろ紙ホルダーを準備する際、手で押し込んで作製していた。
1測定で70個使用するため、その数のホルダーを作製すると手が痛くなり、作業スピードも落ちる。改善後(対策)プラスチック板を挟んで、押し込むことで手の痛みを軽減できた。
プラスチック板はろ紙ケースのフタを再利用した。(ゴミになるもの)効果・継続して作業できる。
・苦悶の時間を削減でき、作業時間を10分程度削減
2020年8月 -
ラベリングでファイル管理
-
改善前(問題点)各記録書類が社名ごとに分けられており、保管期間を過ぎた書類を処分する際、年度を見て手作業で抜き取って作業を行っていた。改善後(対策)年度ごとの「あ行」「い行」「う・え行」「お行」のように分けた。これにより書類を処分する際は、該当年度のファイルごと抜き取ることができるようになった。効果【生産性】
改善前処分する書類を探す時間
約2時間×5日=約10時間
【コスト】
2300円×10時間=23,000円 23,000円down
2018年11月 -